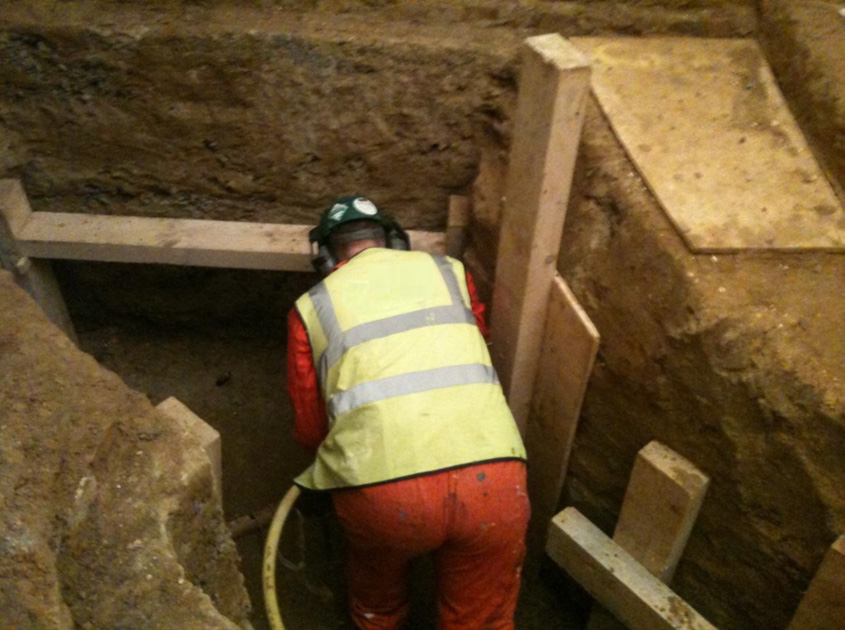
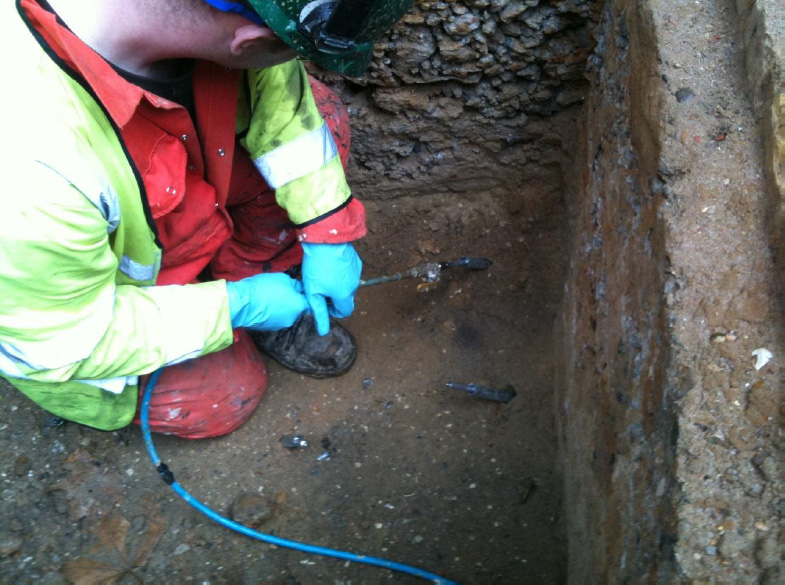
Ground Stabilisation for a London Construction Contractor
When it comes to intricate excavation projects in densely built urban environments, ensuring ground stability is paramount. A recent project in Westminster demonstrated Total Specialist Maintenance’s expertise in meeting this objective as well as our ability to manage the sensitivities of a site of historical and political importance. It was essential that works did not alter or damage the building on site, or the adjacent party wall to the west.
Working in support of a London Construction Contractor, we were tasked with stabilising the ground for a basement extension of a Grade II listed building. Total Specialist Maintenance (TSM) successfully implemented an advanced polymer injection system to ensure a safe and efficient excavation process.
The Challenge
The project involved excavating a two-storey basement beneath the listed building while ensuring minimal ground movement. Given the site’s close proximity to neighbouring properties, traditional excavation support methods such as bored or sheet piling were not feasible. The primary concerns were:
- Unstable sandy and gravelly soil (Lynch Hill Gravel)
- High groundwater levels leading to potential excavation instability
- The risk of ground movement impacting adjacent structures
- Strict environmental and heritage preservation requirements
Why Ground Stabilisation?
After evaluating multiple options, including sheet piling and bored piles, TSM determined that a polymer-based injection system was the most viable solution. This technique provided several advantages over conventional stabilisation methods:
- No mechanical noise or vibration – Essential for preserving nearby heritage structures
- Enhanced soil strength – Polymer injection transformed loose sands into a rock-like material
- Waterproofing properties – Preventing groundwater ingress during excavation
- Accelerated project timelines – Stabilisation work progressed simultaneously with excavation
The Solution: Advanced Polymer Injection
TSM deployed MC-Injekt 2700, a high-performance polyurethane injection foam, to stabilise the ground. This solution offered a range of attributes which is ideal for injection grouting: as well as being solvent-free, low in viscosity and low density, it achieves good penetration into cavities and bonds to wet surfaces. The foam stops water under pressure, does not shrink and can be injected against flowing water.
- Surface Injection: Injection probes were driven into the soil at 500mm intervals, ensuring deep penetration of the stabilising agent.
- Shallow Excavation: A small section of stabilised soil was carefully removed to test stability.
- Side-Wall Injection: Additional polymer was injected into the exposed excavation walls to reinforce the structure as work progressed.
This staged approach allowed for rapid yet controlled excavation, significantly reducing the risk of collapse or soil movement.
Handling the Sensitivity of the Location
Due to the presence of security checkpoints related to the site’s architectural and political importance, along with the stringent planning regulations governing listed buildings, TSM adopted meticulous planning and execution strategies to minimise disruption.
- Vibration-Free Work: The polymer injection method was selected to eliminate any potential for vibrations that could have impacted the delicate structural integrity of surrounding properties.
- Close Coordination with Authorities: TSM maintained active communication with heritage conservation bodies, site security teams, and local authorities to ensure compliance with preservation requirements.
- On-Site Monitoring: Ground movement was tracked through weekly surveys, ensuring that excavation remained within the strict tolerance of 10mm. This level of precision was essential to protect both the existing building and adjacent structures.
- Minimal Overground Disruption: Unlike conventional piling, which requires heavy machinery, TSM’s approach significantly reduced the need for large-scale equipment, thereby minimising noise, logistical constraints, and impact on site security.
Environmental Considerations
Given that the Lynch Hill Gravel is classified as a Secondary Aquifer, it was essential to use an environmentally safe stabilisation method. MC-Injekt 2700 is:
- Solvent-free and approved for use in contact with potable water
- Inert once cured, ensuring no contamination risks
- Minimal waste, with excavated material classified as non-hazardous
Additionally, the polymer injection method had a lower carbon footprint compared to piling alternatives, requiring fewer heavy machinery movements and less fuel consumption.
Ensuring Structural Integrity
To guarantee that adjacent buildings remained unaffected, TSM implemented weekly ground movement surveys throughout the project. The results confirmed that movement never exceeded the tolerance limit of 10mm—an impressive achievement in such challenging ground conditions.
Project Management Excellence
With the project’s tight deadlines, TSM ensured seamless coordination with other contractors on-site. A dedicated technician remained on-site full-time, making real-time adjustments as necessary. Senior management also conducted regular site visits to oversee progress and address any challenges proactively.
Client Testimonial
‘When faced with the complex problem of completing a large excavation in unstable sands and gravels next to a Grade II listed building, we wanted to ensure that we could use the best methodology and personnel to provide a solution. For the deep excavation section in the northwest of the site, we realised conventional piling methods would not be appropriate due to the limited space and proximity of existing buildings. We knew that some form of ground improvement would be necessary, but were unsure as to the best method and product. Our primary concerns were the protection of the existing buildings and the general environment; the speed of the works; and the health and safety of the ground-workers. TSM was able to provide us with a solution that addressed all of the above concerns. The trial undertaken prior to commencement of the project showed us how successful the polymer injection system was, and reinforced our confidence in using the system on a larger scale. Throughout the works, the TSM Technicians and Management team provided a superb service, by ensuring the ground stabilisation was undertaken integrally with other parts of the construction works. The team really knew their trade and were able to react according to the ground conditions uncovered as the excavation progressed. The excavation and underpinning works were able to be advanced rapidly and efficiently, and the primary aim of stopping ground movement to protect the existing buildings was achieved. Well done TSM!’
London Construction Contractor
TSM’s successful execution of this project underscores our position as a leader in ground stabilisation and specialist construction solutions. By leveraging cutting-edge polymer injection technology, TSM not only overcame technical challenges but also maintained best practice for excavation safety and efficiency in historic urban environments.
For more information on TSM’s ground stabilisation and other specialist services, visit www.totalsm.co.uk.
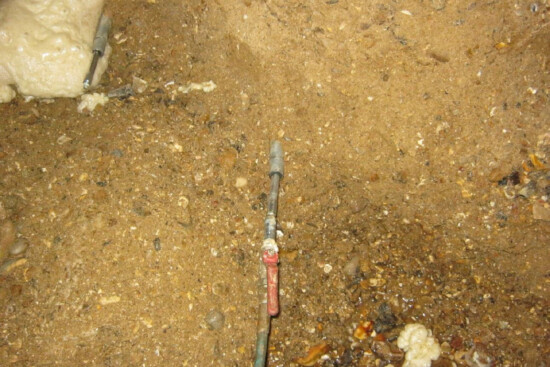
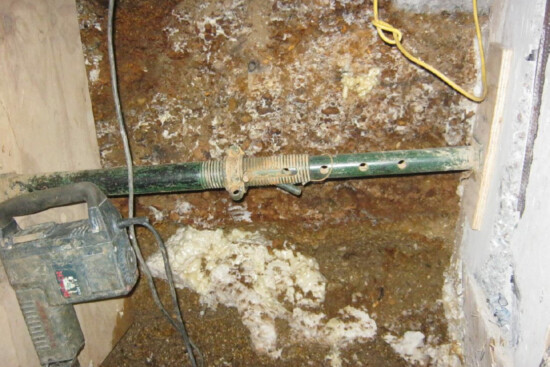
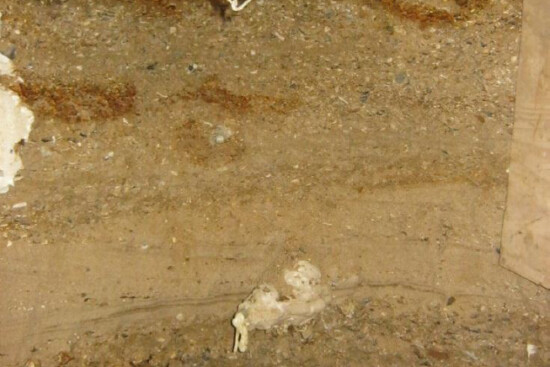
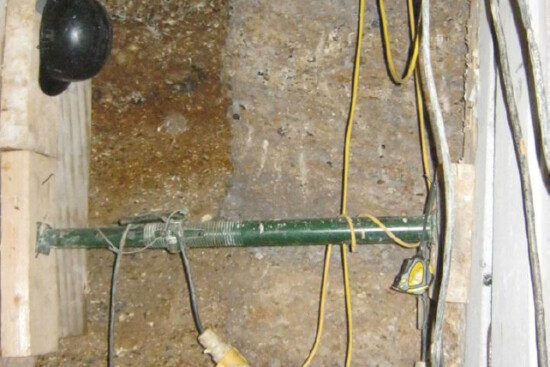
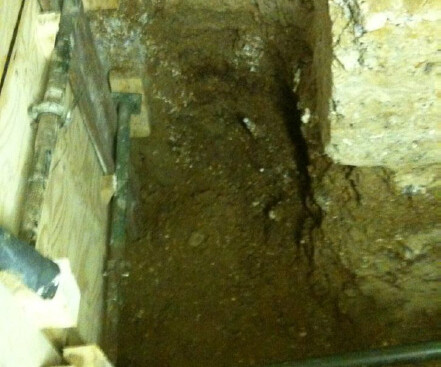
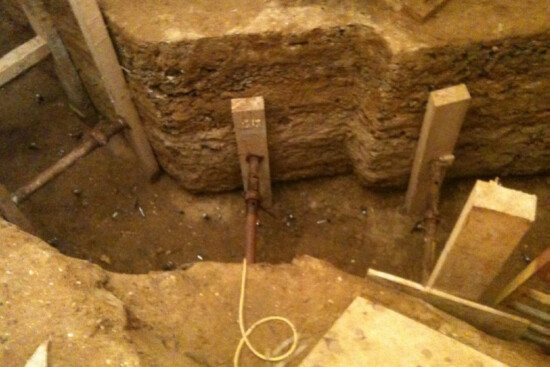
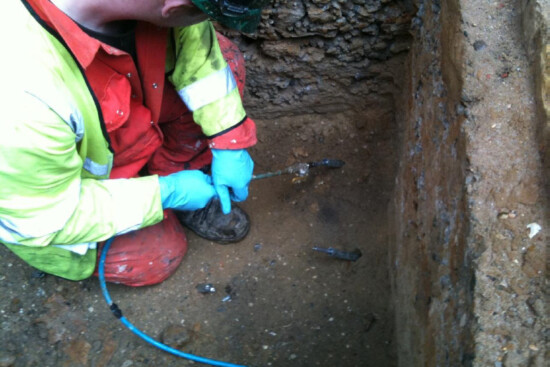
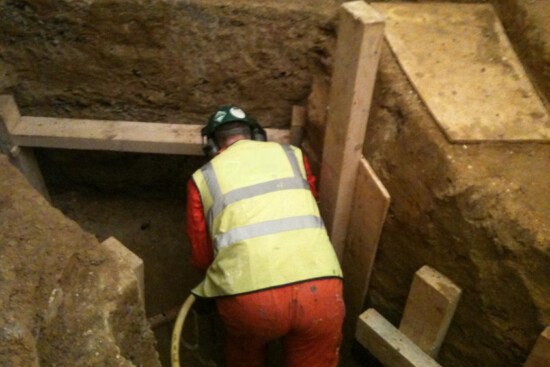
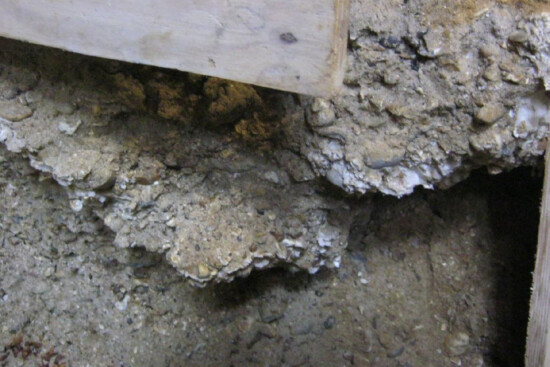
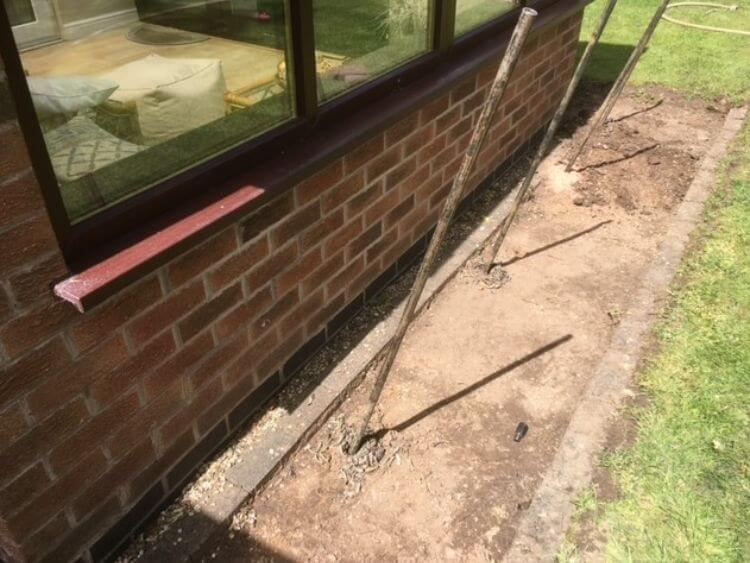
Ground Stabilisation for a London Construction Contractor
The conservatory/ extension was suffering from subsidence with a detaching effect away from the main structure of the house.
The works involved driving injection lances 2 meters underneath the perimeter foundation. Once installed, the injection were then injected with a structural polyurethane ground stabilisation geopolymer resin. During the process the injection lances were extracted at 150mm increments to guarantee continuous placement of the geopolymer.